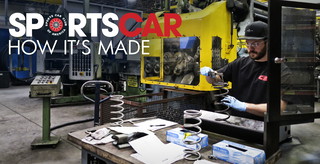
This article first appeared in the July, 2016 edition of SportsCar Magazine. SCCA members can read the current and past editions of SportCar digitally here after logging into their account; To become an SCCA member and get SportsCar mailed to your home address monthly in addition to the digital editions, click here.
We tour a manufacturing facility we didn’t know existed and learn that racecar springs, dampers, and swaybars are made in a way we didn’t know possible
The door opens on an otherwise ubiquitous looking warehouse in Corona, Calif. – a warehouse you might otherwise assume is simply a distribution hub for this international suspension company – and we step inside. But while this massive building does house products ready to ship, it’s also where Eibach Springs manufactures the vast majority of its springs, swaybars, and coilover systems that customers purchase in the U.S. It’s also the starting point for the question that brought us here: How are automotive springs manufactured? The answer, we discovered, is somewhat surprising.
While an increasing amount of the manufacturing process is automated, a significant portion requires hands-on interaction by Eibach’s staff, both in setup and quality control. On top of this, we discovered, there are a lot of preconceived notions about spring manufacturing that are either no longer true, or perhaps never were.
For starters, you won’t find a massive oil bath where springs are dumped after being superheated and bent into their springy form. To be honest, we were expecting a medieval foundry in this regard. But, while you might see that at some point in Eibach’s manufacturing process, it’s the exception rather than the rule, and probably doesn’t apply to your competition or street car parts at all. The realities of spring manufacturing are a little less flashy, but just as effective.
“A spring’s life starts as raw steel,” explains Mark Krumme, who heads the marketing department for Eibach, and is also a bit of a car nut himself. “We keep about 600 metric tons on hand at all time. Since we only order from a few suppliers for the sake of product consistency and quality, we have to keep at least a six-month supply of wire on hand.”
Standing amid these massive bales of raw wire is somewhat frightening, as the unimaginable amounts of potential energy wound into tall circles of steel is intimidating. As we walk through aisle after aisle of these steel bales, Krumme assures us we needn’t worry – a multitude of precautions are taken to keep the entire process safe.
“The wire then goes over to a proprietary Wafios winder, a machine that was designed to our specifications,” Krumme continues, noting that the same machines that wind Eibach’s street springs also wind intricate race springs for both your average SCCA racer and NASCAR.
The now recognizable automotive springs then move to a massive tempering oven, which looks like a stumpy, exceptionally reinforced shipping container. Once inside, the springs are heated and cooled, setting the steel into its new shape. The springs then head to finishing, where a chamfer can be added or the ends ground, depending on the application.
Shot peening comes next. “This removes the outermost layer of material and is basically like a forging process to strengthen the material,” Krumme explains. “After this, you have a much stronger spring.”
From this massive industrial machine, a box of springs is wheeled about 20 feet to the presetting department. There, a person takes each spring, places it in a comparatively small machine, and compresses the spring until the coils bind – otherwise known as hitting block height.
“This basically sets the height of the spring for the duration of its life,” says Krumme. The spring loses a small portion of its height here, but that’s all worked into the equation in the engineering.
Next is the dress-up portion, involving a chemical bath and powder coating, which is followed by a quality check. “The last step is bringing the springs into the quality check department,” says Krumme. “They’re measured, rated, and tested.” Truth be known, this is actually the second quality check, as the initial check happens right after the springs come off the Wafios.
During that quality check, Eibach is looking for no more than an extremely minimal variance on the target spring rate. If you’re looking for a tighter spread, Eibach offers its Platinum line, which boasts half a percent variance. “Our Platinum race springs are made from a super high tensile material and the spring winding technology makes them extremely compliant,” Krumme says. “They’re lightweight and give you a lot of control, and we provide a dyno chart for each one of these springs.”
Eibach also produces its swaybars in house, which makes sense when you realize the production process is all but identical to that of a spring, albeit on different machines. The swaybars are made from spring steel, so they follow the same basic production methods. “They’re bent, taken to end forming, then tempered and shot peened,” he says. During the process, quality control checks are made. “Swaybars get jigged up after the first bend and after the end forming,” Krumme tells us, “and then those get their turn in the quality control department, too, before leaving the building.”
Around the corner from all of this, in the same innocent looking warehouse, is damper production. “We have mild steel and stainless steel tubes,” Krumme explains of the process that turns metal tubes into finished dampers in a surprisingly small corner of the warehouse. “For the stainless, we’ll TIG on the end caps, and for the mild steel, we super heat the end and smash it shut. After that, they all get pressure tested.”
From there, a CNC machine either cuts threads onto the body or places a circlip mount, and then the body heads to the coating department. “For some mild steel, we shot peen them and then have them powder coated, while others get sent to zinc,” explains Krumme. “For stainless, we get them electro-polished. Then they go into assembly.”
The assembly procedure begins with honing the innards of the damper so it seals correctly to the gas piston o-ring and the piston wipers, then the internals stuffed inside the body by a machine that does said stuffing and oil filling in one fell swoop. Meanwhile, anything with a shrader valve or that’s a coilover gets assembled by hand.
Like the springs and swaybars, the shocks also go through quality control, where every shock is tested on a dyno.
It turns out, not every component that leaves this facility does so with an Eibach logo painted on the side – Eibach private labels components for a number of manufacturers. But it’s not just other aftermarket companies that use Eibach’s facility for its products, oh no. “Companies like McLaren, Lotus, Ferrari, Lamborghini, Audi, and Porsche are all looking to us for the private labeling of parts,” Krumme says.
As we head back out of the facility, winding past the salt bath machine where prototype parts bathe for more than 500 hours, and near the machine that puts the same springs through a torturous multi-hundred-thousand compression thrill ride, we find ourselves awed by how much the entire process makes perfect sense, when you think about it. At the same time, we find ourselves pondering all kinds of other questions, like shot peening and tempering – how the heck does that work?
Words and Photo by Philip Royle