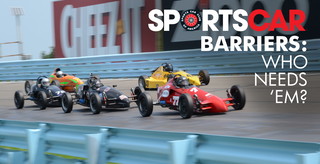
This article first appeared in the August, 2016 edition of SportsCar Magazine. SCCA members can read the current and past editions of SportCar digitally here after logging into their account; To become an SCCA member and get SportsCar mailed to your home address monthly in addition to the digital editions, click here.
Impact barriers have come a long way since the days of hay bales and half-submerged tires – and the development continues
There’s an old joke among race drivers that says excessive speed will never hurt you – it’s the sudden stop that does. Like most dark humor, it’s funny because it’s true. Nothing good happens in a crash, and if you crash into something heavy and hard, it’s even worse for your car and your body.
From the beginnings of automobile racing, drivers and organizers recognized that some kind of barriers were necessary in key places around any given racecourse. In the early days, most road racing circuits were just country roads or city streets blocked off for the big day. A few bales of straw were generally placed between the racecourse and corner workers, starters, and spectators, but races were often held without even that much protection. The lack of safety barriers between spectators and cars led to some of racing’s darkest moments in that era.
“Don’t discount the early use of earth as a ‘safety’ barrier,” recalls longtime SCCA racer and safety advocate Jim Downing. “One of the early reasons for the invention of the HANS Device was because of Patrick Jacquemart’s fatal accident into the earth bank at Mid-Ohio in 1981. I also recall serious accidents at Sebring in the 1950s and ’60s at the hairpin, which ended in an earth bank. I was there starting in 1956 as a young spectator.”
In addition to hay bales, early racecourses abounded with hazards including trees, houses, phone poles, and ditches by the road. In 1966, after a devastating crash through a phone pole and into a farmer’s barn, Formula 1 driver Jackie Stewart began to agitate for better track safety. "We were racing at circuits where there were no crash barriers in front of the pits, and fuel was lying about in churns in the pit lane. A car could easily crash into the pits at any time. It was ridiculous,” Stewart explained.
Finding Improvements
As time went on, purpose-built racetracks replaced street courses. With the ability to design and improve a dedicated facility, racers began to improve their barriers. Freeway-style overlapping guardrails, frequently known by the trade name “Armco” became popular. Guardrails were often used with straw bales placed in front of the rail to provide some additional cushion in the event of a crash.
In the 1970s, flag stations were often protected by 55-gallon drums. These would be half-buried standing up, and then filled with sand for additional mass. A similar design is known as a Fitch Barrier, which is a plastic barrel filled with sand, or sometimes water. The inventor of the Fitch Barrier, John Fitch, was an SCCA racer and, like Jim Downing, is a member of SCCA’s Hall of Fame.
Another development in this period was the tire wall, created from used tires by bolting several stacks of tires together into a unit weighing several hundred pounds. By arranging the tire units with some space to move, a tire wall offers a more compliant barrier than an earthen bank or a length of guardrail.
“The banded tire wall is a reasonable solution, cost-wise when that’s necessary, and it usually is,” Downing says.
Among the most common barriers in use today is the Jersey Wall, also known as K-rail in the western states. Most often made of concrete, these barriers are designed to deflect a vehicle in a shallow angle collision. Loops of cable, cast into the concrete at either end, allow the barriers to be fastened together to produce longer lengths of wall.
All these developments helped to increase the safety of drivers and workers, and as a side benefit reduced damage to cars. Today, the FIA enforces strict standards for runoff surfaces, curbs, and barriers before a track can be certified for competition. The FIA regulations state in part, “As a general principle, where the estimated impact angle is low a continuous, smooth, vertical barrier is preferable, and where it is high energy dissipating devices and/or stopping barriers should be used, combined with a run-off area and deceleration system if there is sufficient suitable ground available.”
Energy Dissipating Barriers
The effort to improve safety barriers continues, and developments in the last 20 years have greatly advanced the science of crash barrier design. In the late 1990s, some tracks adopted a system called Polyethylene Energy Dissipating System (PEDS) that consisted of large pieces of polyethylene foam placed along the wall and bound together. But a 1998 crash by Arie Luyendyk during an IROC race showed that the PEDS could bounce a car back across the track, and the foam pieces came apart under the heavy impact, creating debris.
Oval tracks have since gravitated toward a design known as the Steel and Foam Energy Reduction (SAFER) barrier. Created by researchers at the University of Nebraska, this design uses closed cell foam cushions placed behind a wall made of square steel tubing. The SAFER barrier works because the metal surface will deform and the foam will absorb the force of impact in a high-speed collision.
Similarly, Tecpro barriers are used by Formula 1 tracks around the world. This design uses a foam-filled plastic shell with a central metal plate for reinforcement. Three nylon straps connect each section of barrier to its mates. Additionally, hollow plastic shells are used behind the Tecpro wall to absorb energy.
In every type of crash barrier design, the goal is the same: to dissipate the energy of an impact over time and space to protect the driver and control the motion of the vehicle.
“They’ve got great technology that absorbs a lot of the initial energy that snaps the driver’s head – I think that’s wonderful stuff,” Downing says.
Development continues
Richard Valentine is a longtime SCCA member, a professional racer, and a keen advocate for driver safety. Valentine is also the founder of Impact Safety Systems and inventor of the ProLink Barrier, a new form of energy dissipating crash barrier. The ProLink system is designed to bring the best aspects of all prior barriers together by providing the necessary cushioning effect in a configurable and connected package.
“The whole idea is to give a softer landing,” Valentine explains.
The ProLink design is a series of hollow plastic barrier segments that fit together like a chain, with a tough plastic anchoring pin between segments. Once assembled, each segment can be filled with water to add weight. There is no limit to the number of barrier segments that can be connected, and the amount of water can be adjusted to provide varying amounts of resistance based on the barrier location.
“When they’re linked together, they have a cumulative pull,” Valentine explains. “The barrier gives you cushion when you hit it, but it drags the other barriers along, too.”
Valentine makes his barrier segments from a thick composite plastic that stands up to impacts without cracking or shattering. Because the segments are modular, ProLink allows for any configuration including curves, 90-degree angles, and even switching course directions. The system is also designed to be stackable for storage.
“They’re just plain easier,” Valentine says. “Our barriers are extremely portable [and] lightweight when empty, with quick-release PVC anchoring pins, all of which makes deploying fast and simple. And, they reduce delays during crash cleanup — one worker can replace a barrier in less than 10 minutes.”
From an SCCA perspective, one of the innovations Valentine has developed is a low-profile version of the ProLink barrier suitable for use in setting up Karting or Solo courses.
“If you use them to set up an autocross course, you can put directional arrows or brake markers in the pins. You can reconfigure these for any course design you want,” Valentine says.
ProLink is already installed at tracks including Thermal Club, Thompson Speedway, and Inde Motorsports Ranch.
Looking to the future, Valentine is developing a new foam-filled barrier system that will deliver even higher levels of protection. Prototypes are being made now, and Valentine says they will be available in both soft and hard versions.
According to Valentine, “Hitting these new barriers will be like hitting a pillow!”
The work to make racing safer never ends – and that’s as it should be. As tracks become safer for both human bodies and racecars, drivers will be able to push harder and challenge their skills in a safer environment.
Words by Jeff Zurschmeide
Image by Anthony Bristol